摘要:以高鋅Mg-14Zn-3Al鎂合金為研究對象,利用OM、XRD和SEM等研究了擠壓鑄造工藝對Mg-14Zn-3Al鎂合金的顯微組織、鑄造缺陷和力學性能的影響。結果表明,擠壓鑄造后的Mg-14Zn-3Al合金的顯微組織由α-Mg基體、狹長的塊狀τ-Mg32(Al,Zn)49相、顆粒狀或骨骼狀的ε-MgZn相組成。隨著擠壓鑄造壓力不斷增加,合金組織得到細化,第二相的數(shù)量增多,顯微縮松得到抑制,鑄件中的縮松面積從15.67%急劇減少到0.81%。經(jīng)過擠壓鑄造處理后,Mg-14Zn-3Al合金的抗拉強度、伸長率分別達到218.1 MPa、5.2%,合金的力學性能得到明顯改善。
鎂及鎂合金具有密度低、比強度和比剛度高、減震性好、電子屏蔽性能優(yōu)異及易回收等特點,在汽車、電子、航空航天、國防軍工等領域具有重要的應用價值和廣闊的前景。其中,Mg-Zn-Al(ZA)系合金具有高溫性能好、鑄造性能優(yōu)良,生產(chǎn)成本較低等優(yōu)點。研究表明,通過改變Mg-Zn-Al系鎂合金中的Zn含量、適當控制W(Zn)/w(Zn)質(zhì)量比,可以提高合金的耐熱性能和高溫抗蠕變性能,這是因為Mg-Zn-Al系鎂合金微觀組織中的共晶化合物相主要是熱穩(wěn)定性較強的τ-Mg32(Al,Zn)49(熔點為535℃)相、?-Al2Mg5Zn2(熔點為393℃)或ε-MgZn(熔點為347 ℃)等耐熱的合金相[4~6]。當合金中w(Zn)/w(Zn)比≥2時,尤其是高鋅含量的Mg-Zn-Al合金(如ZA102、ZA122、ZA122)中形成的共晶化合物相主要是熱穩(wěn)定性較強的Mg32(Al,Zn)49相和ε-MgZn相,合金的耐熱性能和抗蠕變性能較好,是新的高鋅耐熱鎂合金。然而,傳統(tǒng)鑄造過程中存在的鑄造缺陷(如縮松)仍然是影響Mg-Zn-Al合金進一步應用的約束因素。
擠壓鑄造是一種結合鑄造和塑性加工特點的短流程、高效、精確成形金屬加工技術。熔體在凝固過程中始終受到壓力作用,一方面有利于晶粒細化,另一方面實現(xiàn)鑄件凝固過程中的強制補縮,可以減輕或消除由于熔體中氣體和凝固過程中的收縮所引起的鑄造缺陷,獲得的鑄件組織致密度高。針對Mg-Zn-Al系合金存在的縮松缺陷,增加壓力可以有效地消除合金鑄件中的鑄造缺陷,提高鑄件致密性、提高鑄件的力學性能。
為了消除高鋅含量的Mg-Zn-Al合金中的縮松等鑄造缺陷,發(fā)揮該系列合金的良好鑄造性能、耐熱性能和抗蠕變性能,本課題以Mg-14Zn-3Al合金為研究對象,研究了擠壓鑄造對Mg-14Zn-3Al合金的顯微組織、顯微縮松和力學性能影響,以期為合金的實際應用提供參考。
1、試驗制備與設備
試驗合金為Mg-14Zn-3Al(ZA143)合金,原材料(質(zhì)量分數(shù))為工業(yè)純鎂(99.9%)、工業(yè)純鋅(99.9%)和工業(yè)純鋁(99.9%)。在720~740 ℃熔化,采用CO2+SF6混合氣體保護,澆注成Ф50 mm×130 mm的圓錠。擠壓鑄造試驗中,將熔煉好的合金熔體在氣體保護下,澆注到預熱為200℃的模具(Ф50 mm×130 mm)中,同時啟動液壓裝置對合金熔體進行加壓,采用單向擠壓,沖頭下行速度為5 mm/s,保壓時間為60 s;對合金熔體施加的壓力分別為0、40、80和120 MPa。
不同擠壓壓力下的金相試樣是在距離鑄錠底端20 mm處截取,隨后對該面進行研磨、拋光,使用體積分數(shù)為4%的硝酸酒精溶液腐蝕表面。拉伸試驗在AG-100kNG型萬能電子實驗機上進行,拉伸試樣在鑄錠橫截面1/2半徑處用線切割截取,并按照GB228.1-2010規(guī)定進行加工,拉伸速率為2mm/min;用GX71Olympus型金相顯微鏡觀察合金的金相組織;用XRD-7000X-射線衍射儀分析合金的相組成;用ΣIGMA型掃描電鏡對試樣進行顯微組織觀察及斷口分析;采用能譜分析儀EDS(X-Maxn)分析合金的微區(qū)成分。
2、試驗結果與分析
2.1 Mg-14Zn-3Al合金的顯微組織分析
Mg-14Zn-3Al合金的鑄態(tài)顯微組織見圖1,可以看出,合金組成為灰白色的α-Mg基體、晶內(nèi)的顆粒狀或孤島狀相、沿著晶界分布的深灰色的狹長塊狀相。同時,在合金中出現(xiàn)了沿晶界分布的顯微縮松(見圖1b)。
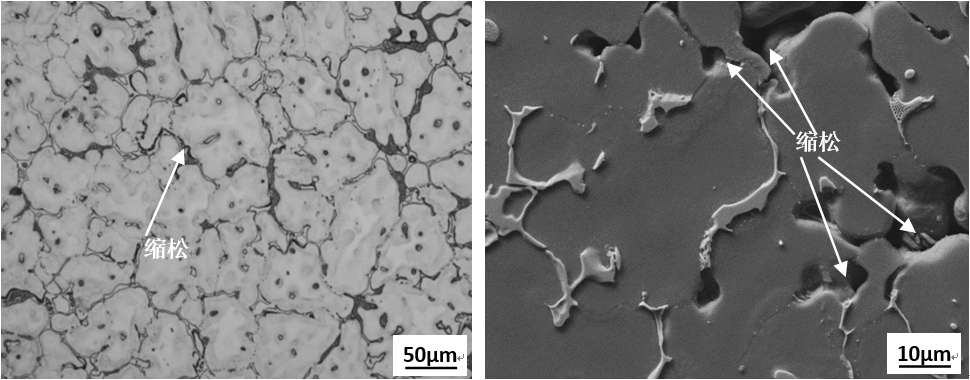
(a)金相組織 (b)顯微縮松
圖1:ZA143合金鑄態(tài)金相組織
圖2為鑄態(tài)ZA143合金的SEM形貌和各點的EDS分析。從見圖2a可清晰顯示合金組織中的各相形貌;由鑄態(tài)合金組織中的點A和點B可知,第二相中除含有少量Al元素外,主要由Mg、Zn元素組成,其化學組成接近ε-MgZn相組成,主要以顆粒狀或有致密層的骨骼狀存在,見圖2a和圖2b;圖C點的狹長的塊狀相中該相Zn、Al含量高于Mg,其成分接近τ-Mg32(Al,Zn)49相,見圖2d。本試驗結果與楊明波等獲得的結果吻合。
.jpg)
.jpg)
圖2:鑄態(tài)ZA143合金的SEM形貌和各點的EDS能譜圖
為了進一步明確ZA143合金凝固組織中的第二相的類型,使用XRD對其進行分析(見圖3)。根據(jù)PDF卡片信息以及對于的衍射峰標定結果可知,在ZA143合金中的主要化合物相為?-MgZn相和τ-Mg32(Al,Zn)49。
.jpg)
圖3:鑄態(tài)的Mg-14Zn-3Al合金XRD圖譜
2.2 ZA143合金在不同壓力作用下的顯微組織變化
圖4為不同擠壓鑄造壓力下的ZA143合金的金相照片??梢钥闯?,不同壓力下的ZA143合金均具有枝晶形貌,其凝固組織均由α-Mg基體、半連續(xù)的狹長塊狀的τ-Mg32(Al,Zn)49相、顆粒狀或骨骼狀的ε-MgZn相組成。當壓力為0(重力鑄造)時,α-Mg枝晶粗大,在晶界處的第二相呈不連續(xù)分布,且面積占比較小,晶內(nèi)同時分布著數(shù)量較少的顆粒狀第二相(ε-MgZn相);當壓力提高到40 MPa時,α-Mg枝晶細化,第二相增多,其在晶界處分布由不連續(xù)分布轉變?yōu)檫B續(xù)分布,晶內(nèi)分布的顆粒狀第二相呈細化趨勢;繼續(xù)提高壓力,α-Mg枝晶細化趨勢變小,第二相在晶界處為連續(xù)的網(wǎng)狀分布。
.jpg)
.jpg)
圖4:不同擠壓鑄造壓力下ZA143合金的凝固組織金相照片
此外還發(fā)現(xiàn),擠壓鑄造壓力為0時,組織中有縮松出現(xiàn)。隨著壓力的增大,即80 MPa和120 MPa時組織中觀察不到明顯縮松存在。
.jpg)
圖5:壓力對ZA143合金平均晶粒尺寸的影響
采用截線法對不同擠壓鑄造壓力下ZA143合金鑄件在1/2高度處沿徑向的晶粒尺寸進行定量金相統(tǒng)計,結果見圖5??梢钥闯觯攭毫?提高到40 MPa,合金凝固組織中的晶粒尺寸明顯減小,但是當壓力從40 MPa提高到120 MPa時,壓力的變化對晶粒尺寸的影響并不顯著。此外,隨著距鑄件表面距離的增加,晶粒尺寸逐漸增加:當壓力為0時,在距鑄件表面5 mm和25 mm處的凝固組織中的平均晶粒尺寸分別為100 μm和160 μm;當壓力為40 MPa時,在上述相同位置處的凝固組織中的平均晶粒尺寸分別為89 μm和111 μm,這表明擠壓鑄造能夠提高合金鑄件的凝固組織的均勻性。
在壓力作用下ZA143合金組織得到細化,一方面是壓力使凝殼緊貼型壁,增加了二者界面的傳熱系數(shù),提高了熔體的冷卻速率,另一方面是壓力引起合金熔體物性參數(shù)的變化,提高熔體凝固過程中的形核率。壓力不僅會改變?nèi)垠w冷卻速率,而且還會改變?nèi)垠w的平衡凝固溫度。壓力對熔體平衡凝固溫度的影響可以用Clausius-Clapeyron方程描述:
.jpg)
式中,Tm為熔體在標準大氣壓下的平衡凝固溫度;Vl和VS為熔體凝固前后液相和固相的摩爾體積;ΔHm為結晶潛熱;dp為壓力的變化。ZA143合金的結晶溫度區(qū)間較寬,傾向于體積凝固方式凝固,提高壓力將使熔體平衡凝固溫度升高,增大了熔體在凝固過程中的過冷度,從而導致晶粒細化。
根據(jù)經(jīng)典凝固理論,金屬液凝固時的臨界晶核半徑rk和臨界形核功ΔG0分別為:
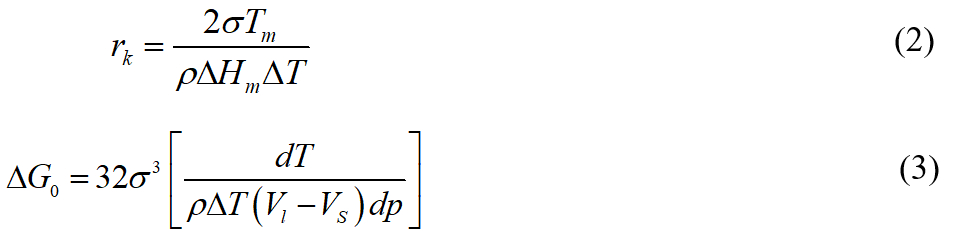
式中,ρ為密度;σ為表面張力;ΔT為過冷度。由式(2)、式(3)可得出,由外加壓力造成的過冷度提高可同時使臨界晶核半徑和臨界形核功減小,使結晶核心數(shù)量增多,促使熔體凝固由均質(zhì)形核向非均質(zhì)形核方式轉變,從而使組織細化。
2.3 擠壓鑄造壓力對ZA143合金凝固缺陷的影響
不同擠壓鑄造壓力下的ZA143合金中的縮松宏觀分布見圖6。隨著壓力增加,ZA143合金中縮松分布的范圍逐漸減小。從圖6a可以看出,沒有施加壓力時,ZA143合金鑄件中的縮松主要集中在鑄件的中上部,兩條縮松聚集“條帶”呈中心對稱分布,而鑄件側面和底面的縮松較少。隨著壓力增加,40 MPa和80 MPa下擠壓鑄造的ZA143合金鑄件中的縮松減少,而且不再呈密集聚集狀態(tài),而是呈面積較大的“V型”分布狀態(tài)。這是由于鑄型表面的激冷作用,鑄件邊緣處的熔體最先凝固形成凝殼,凝殼在壓力作用下發(fā)生塑性變形,使熔體承受等靜壓。在擠壓鑄造的初期,凝殼厚度小,易發(fā)生塑性變形,此時熔體受到的等靜壓大,抑制了縮松產(chǎn)生,因此鑄件側面和底面的縮松較少。但是隨著凝固過程進行,凝殼厚度逐漸增加,凝殼在壓力作用下發(fā)生塑性變形所消耗的能量逐漸增加,鑄件心部熔體承受的等靜壓也就越小,因此鑄件心部容易產(chǎn)生縮松。
鎂合金在凝固過程中易形成發(fā)達的樹枝晶,樹枝晶互相連接形成骨架,將尚未凝固的熔體封閉起來,該部分熔體凝固時發(fā)生體積收縮,而相鄰部位的熔體無法補縮,從而在枝晶間形成縮松。在擠壓鑄造工藝下,如果壓力足以使先形成的凝殼發(fā)生塑性變形,這將使枝晶間液相向著阻力較小的固液兩相區(qū)、液相區(qū)和縮孔區(qū)流動,從而實現(xiàn)了強制補縮。
.jpg)
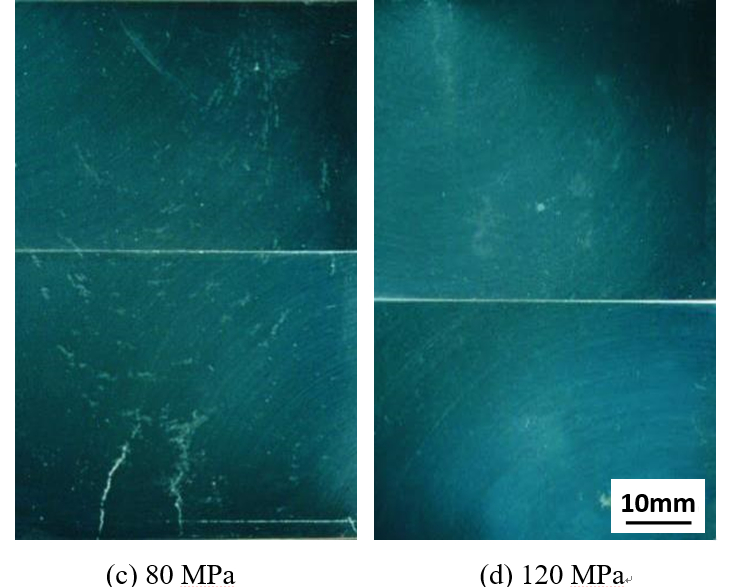
圖6:不同的擠壓鑄造壓力下ZA143合金中的縮松分布
.jpg)
圖7:壓力對ZA143合金中縮松面積分數(shù)的影響
不同擠壓壓力下的Mg-14Zn-3Al合金中存在的縮松面積統(tǒng)計結果見圖7??梢钥闯觯S著壓力增加,ZA143合金中縮松面積逐漸減少。當壓力從0增加到40 MPa時,合金中的縮松面積從15.67 %急劇減少到6.91 %;當壓力增大到80 、MPa120 MPa時,合金中的縮松面積分別減少到2.5 %和0.81 %。
2.4 ZA143合金在不同壓力作用下的力學性能
圖8為不同擠壓壓力下的ZA143合金的典型的拉伸曲線,其對ZA143合金拉伸性能的影響見圖9。當壓力從0增加到40 MPa時,ZA143合金的屈服強度從140.5 MPa降低至113.1 MPa;當壓力繼續(xù)增加到80 MPa時,合金的屈服強度降低到了110 MPa;當壓力繼續(xù)增加到120 MPa時,合金的屈服強度又升至116.5 MPa。屈服強度的下降與晶界處ε-MgZn相和Mg32(Al,Zn)49相增多有關:隨著擠壓壓力增加,晶界處第二相增多,消耗了基體內(nèi)的Zn、Al元素,導致基體固溶強化能力下降,基體更容易優(yōu)先變形,所以屈服強度有下降趨勢。當壓力為0時,合金的抗拉強度和伸長率為192.6 MPa和1.2 %,當壓力提高至40 MPa時,合金的抗拉強度和伸長率分別為205.5 MPa和4.38 %,當壓力繼續(xù)提高到120 MPa時,合金的抗拉強度和伸長率分別為218.1 MPa和5.2 %,分別提高了13.2 %和333 %。隨著擠壓鑄造壓力增加,ZA143合金的組織得到細化,同時又能減少合金的縮松,因此ZA143合金綜合性能得到提高。
.jpg)
圖8:不同擠壓鑄造壓力下ZA143合金的典型拉伸曲線 圖9壓力對ZA143合金拉伸性能的影響
圖10為不同擠壓壓力下的ZA143合金的拉伸斷口掃描電鏡照片??梢钥闯?,當壓力為0時,合金拉伸斷口為解理面、解理臺階及少量撕裂棱,表現(xiàn)出混合斷裂特征,同時,斷口存在明顯的斷裂裂紋(圖10a中箭頭所示);當壓力繼續(xù)增加到40 MPa時,合金拉伸斷口中未觀察到斷裂裂紋,斷口中存在很多較窄的解離臺階、少量的韌窩以及撕裂棱,表現(xiàn)出以韌性斷裂為主的混合斷裂特征;當壓力繼續(xù)增加到80、120 MPa時,合金拉伸斷口中韌窩以及撕裂棱增多,存在較窄的解離臺階,仍然表現(xiàn)出韌性斷裂為主的混合斷裂特征。
.jpg)
.jpg)
圖10:不同壓力下的ZA143合金拉伸斷口掃描電鏡照片
3、結論
(1)擠壓鑄造使得鑄態(tài)ZA143合金組織中α-Mg枝晶得到細化,第二相增多,合金由α-Mg基體、狹長的塊狀τ-Mg32(Al,Zn)49相、顆粒狀或骨骼狀的ε-MgZn相組成,其在晶界處分布由不連續(xù)分布轉變?yōu)檫B續(xù)分布。
(2)擠壓鑄造壓力增加能減少鑄態(tài)ZA143合金中的縮松缺陷,鑄件中的縮松面積分數(shù)從15.67%急劇減少到0.81%。
(3)擠壓壓力的增加提高了ZA143合金的綜合性能,當壓力達到120 MPa時,合金的抗拉強度和斷后伸長率分別為218.1 MPa和5.2 %,較重力鑄造分別提高了13.2%和333%。
作者:
王杰 高恩志
沈陽航空航天大學材料科學與工程學院
周吉學 唐守秋
齊魯工業(yè)大學(山東省科學院)新材料研究所
本文來自:《特種鑄造及有色合金》雜志2020年第40卷第10期